Hi guy's!
Made some progress on a few things today. I'm trying to get everything ready so the next time the crankshaft comes out, I will have everything ready to put it back in for the last time. I made a couple more collets to hold gears for modification. I made one for the idler gears and this one to modify the crankshaft gear.
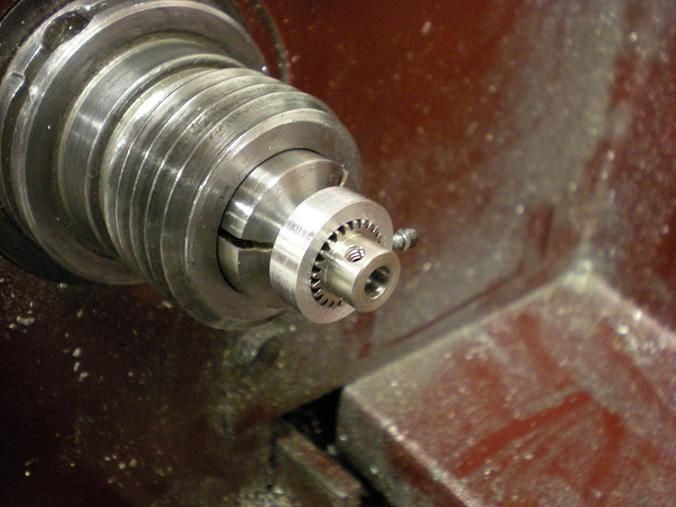
Turned the hub down to the correct thickness. This will put the correct distance between the gear and the bearing.
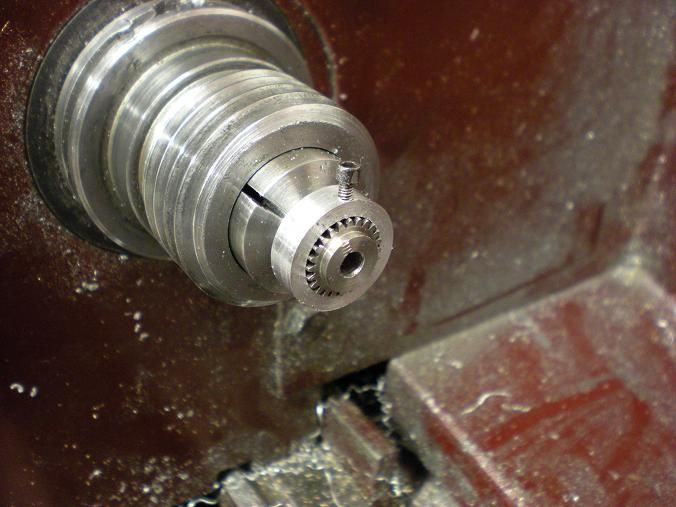
Then the OD was modified to work with the bearing. The bore was opened up to a press fit onto the crankshaft. This finished up the crank gear.
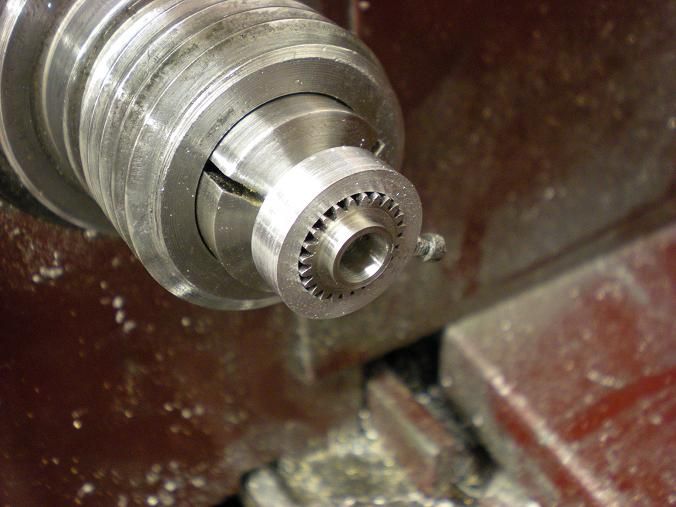
I also made one for the idler gears. The idler just needed the hub removed. I also made the idler mounts. Only one of the idler gears is needed but I wanted to make mine like a Pete Jackson gear drive so i'm going to run 2 idlers.
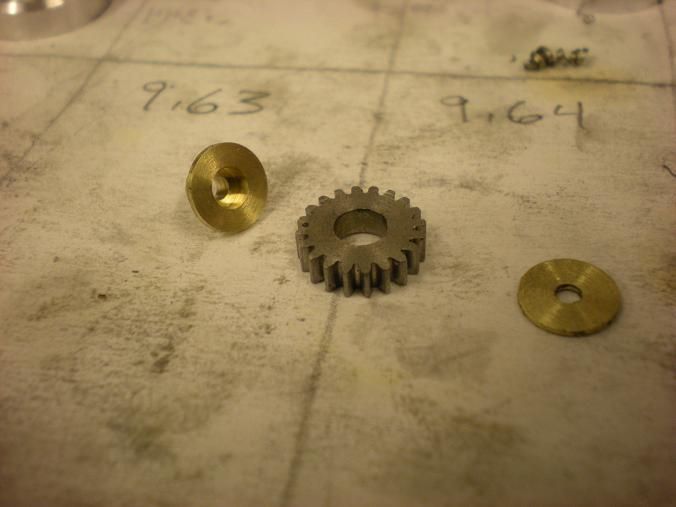
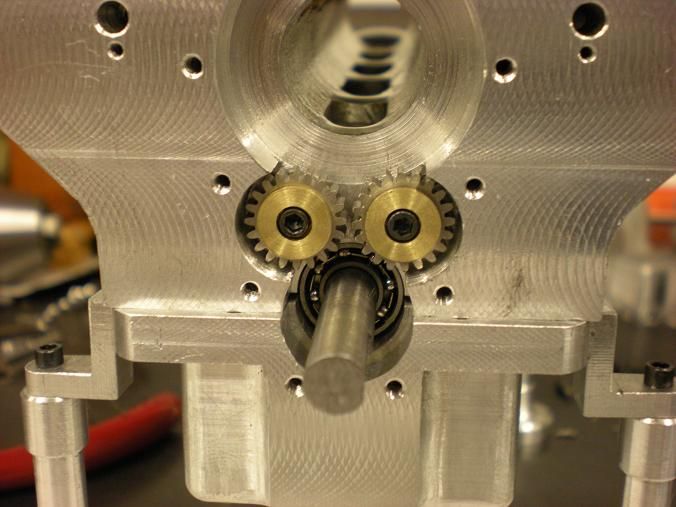
After that I made my fixture for heat treating my rings. This fixture is made the George Trimble way. I included the fixture in the drawings but it is only good for 5/8 rings.
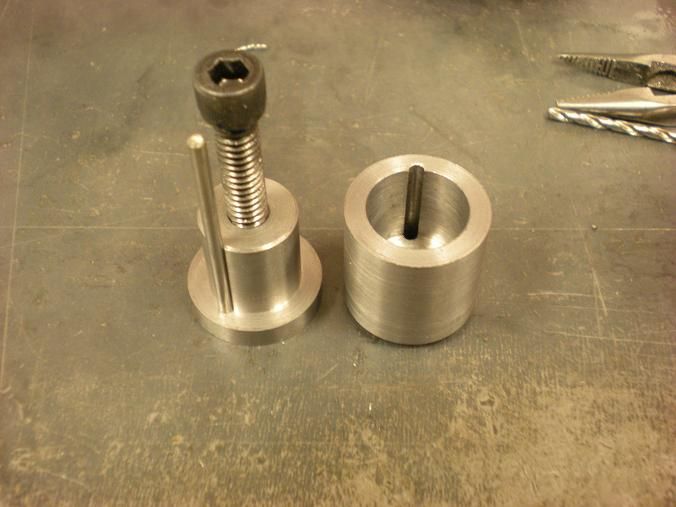
Turned and bored the cast iron for the rings. Finished with 180, 320, and then 600 grit paper. Real happy with the finish and hit my number inside of .0002.
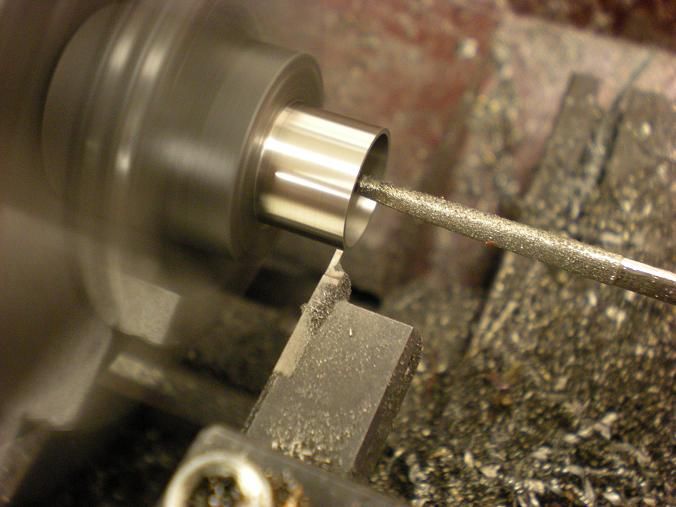
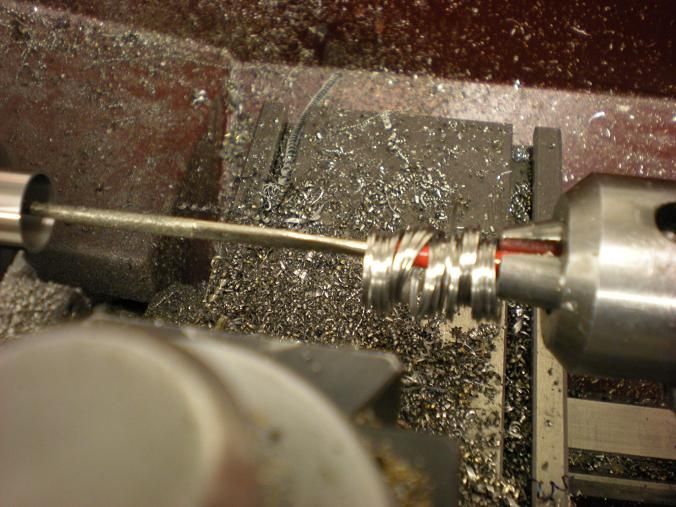
Loaded 27 rings into the fixture and they are ready for some heat.
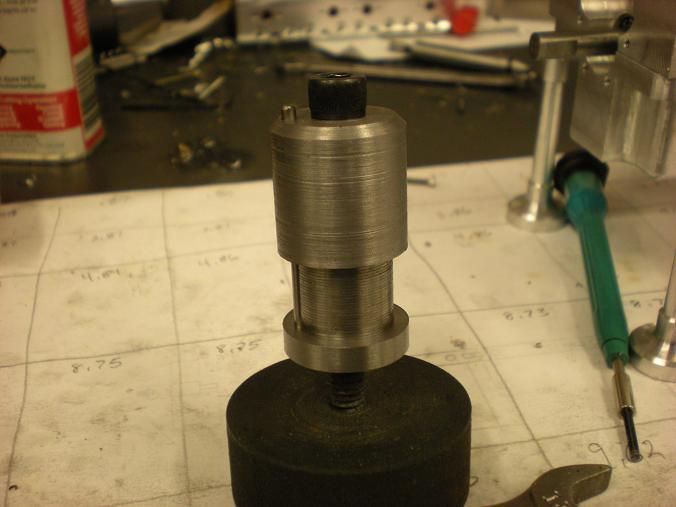