Hi,
Great project, very inspiring!
I have a machine in the making that is surprisingly similar to your machine!
I have a Synrad 48-1 (16W) that I am going to fit on it and regarding the tickle electronics I solved that by asking a friend to program an 8 pin PIC microcontroller to take mach step + dir (or step + laser on), generating the tickle and adding that to the step-pulses. There is also a manual mode where a button sets laser on and a pot or voltage 0-5V sets the laser power for testing or other applications.
It worked right away but might need som tweaking and input from other users to be perfect. My friend also made a pcb for it but I have it on protoboard for now. Drop me a PM if you are interested in testing it, I have much work ahead until it's laser time!
I have been building my machine very slowly for a few years but life, work and kids seem to get in the way all the time...

I'll make a thread about it when I get a little further off the ground so to speak!
This is a pic from february 2008 and not much progress has been made since!

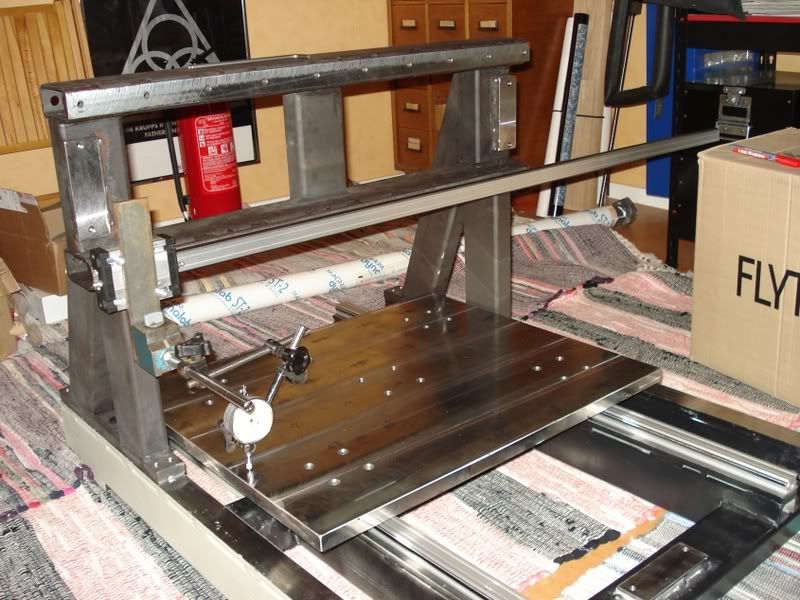
This is my laser with improvised cutting nozzle with 12diameter, 50mm focus lens. The lens is far to close to the laser for optimal cutting cuality but its ok for experimentation.

(sorry for the threadjack, I just saw some (infrared) light in the end of my tunnel!)
