First off a little background for the machine.
It's brand spank new and has been designed as a CNC from day one.
Spindle is driven by a 500 watt 3 phase brushless servo with encoder feedback to the driver board, this then drives thru a 3:1 timing belt reduction so it's at max torque at 800 rpm.
True speed at a requested 800 rpm is 800 to 804 and steady.
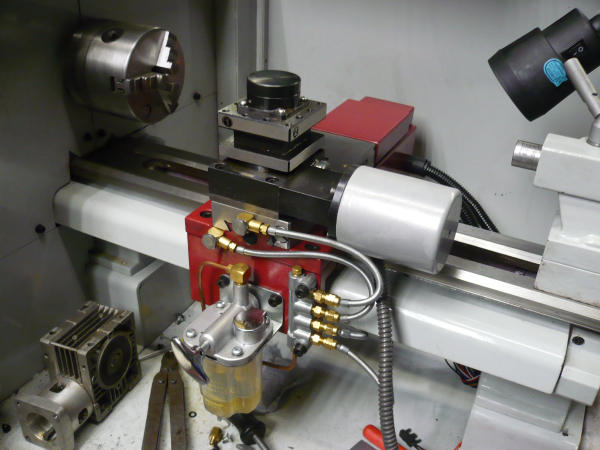
Ballscrews fitted with no discernable backlash, no compound, everything tight.
I'm running the same tests over and over which is a 2mm pitch thread 80 mm long, short threads don't show an error like the long ones and I'm positive that you need to cut long threads and use a tap or known screw as a pitch gauge because a thread gauge fits along the thread due to the fact it only covers about 4 or 5 pitches.
This is what I'm getting for the first three cuts
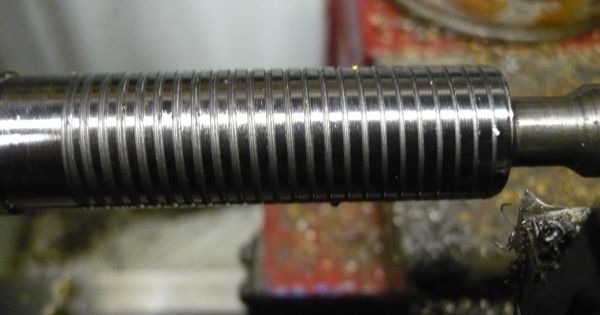
Unlike Steve who was getting a narrow land at the start and end and OK in the middle I always get a good thread at the start and an increased pitch at the end causing the land to become very narrow.
At the end of 80mm I'm about 1/2 a pitch or 1mm out.
Art has picked up on aluminium threads being OK but they were shorter ones for a job.
tomorrow, well later today as it's 1:30 am here I'll cut a long alloy thread with the same driver I have on the machine now.
Then I'll swap to the driver Art has sent and redo the threads in alloy and steel, scratch cuts at first.
John s.