This is the story of how we built one of the largest spinning tools you are ever likely to see. This is a parabolic spinning tool for making aluminium reflectors for satellite antennas and weather radar systems. It weighs around 2.5 tons. We had a 3.0m tool which was bought as part of a factory closure. it had originally been the centre of a 4.5m tool, but the outer segments had been scrapped. so we had to remake them. It was no small job.
fig.1. The 3.0m tool
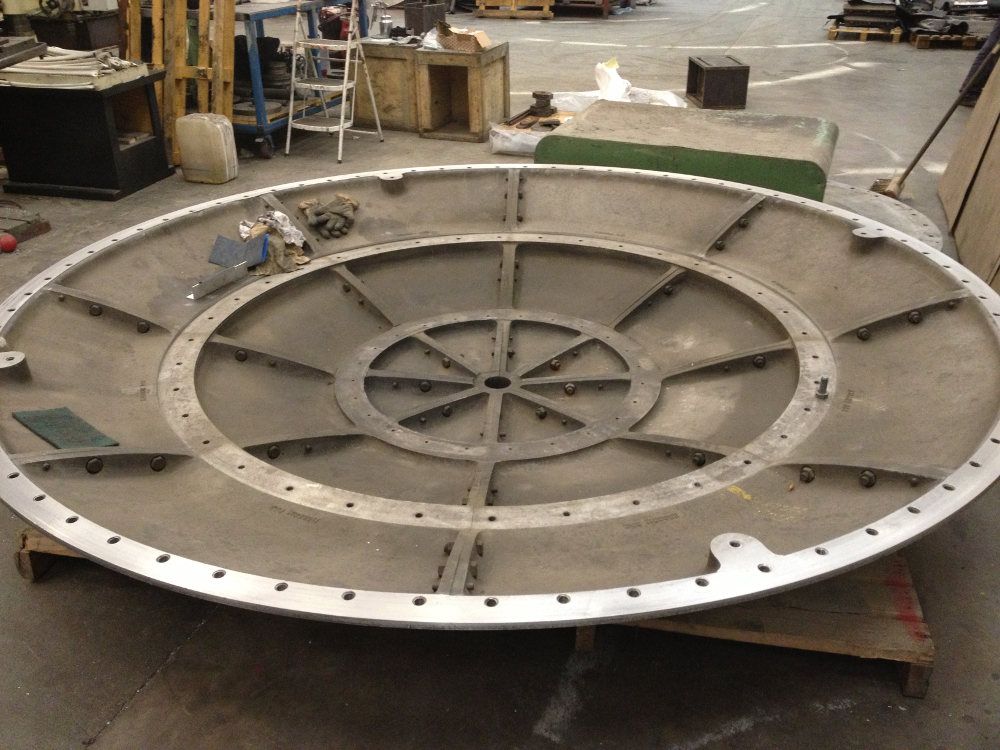
Fig. 2 After making a pattern and having the new segments cast, the machining references were milled and holes tapped for fixturing. They were milled on a large 3-axis machine, tilted as they would be in service to allow the sides to come parallel when assembled.
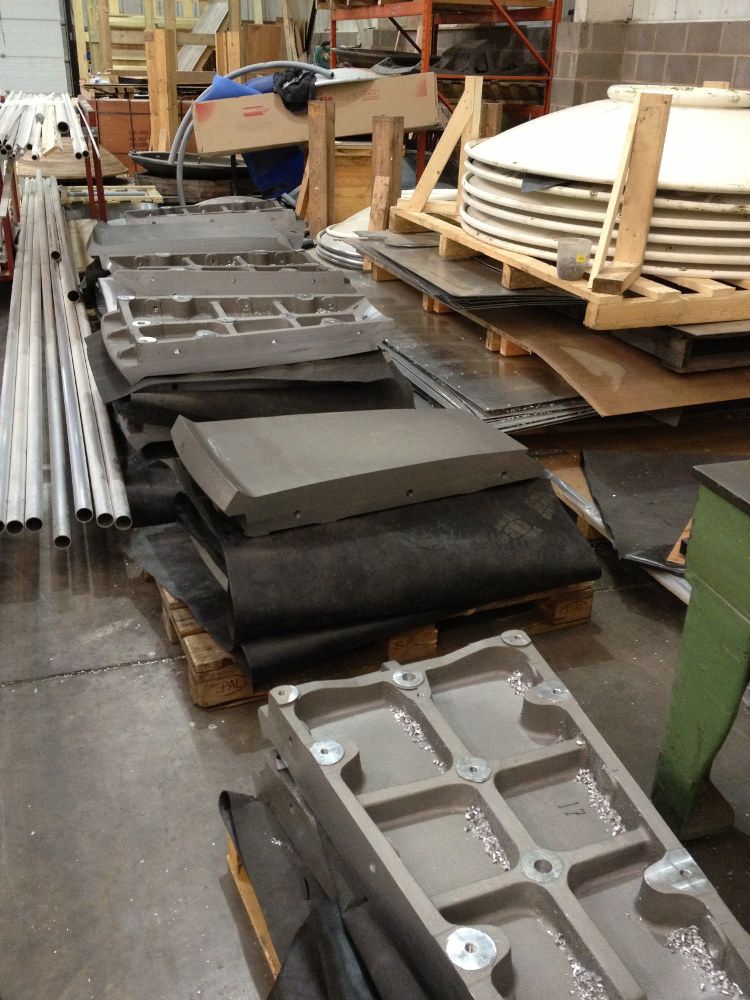
Fig. 3. Assembling the tool for finish turning
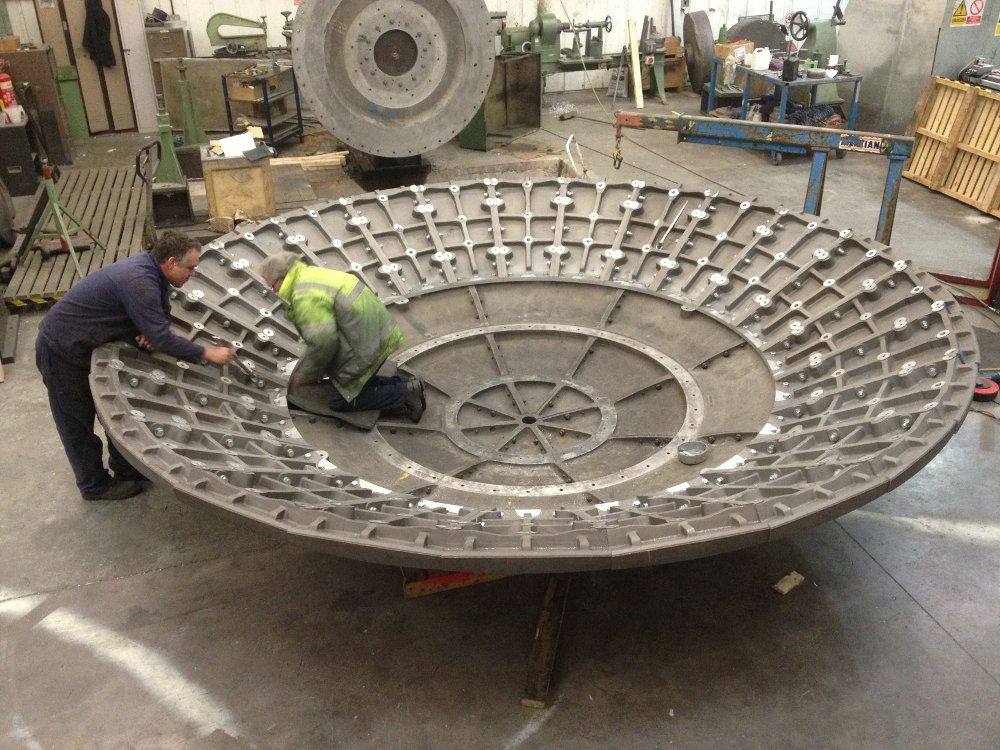
Fig. 4. The tool in position on the lathe headstock where it will be used, driven at around 60RPM using a 20hp motor. Note the pit needed to clear the tool to put the axis at a workable height.
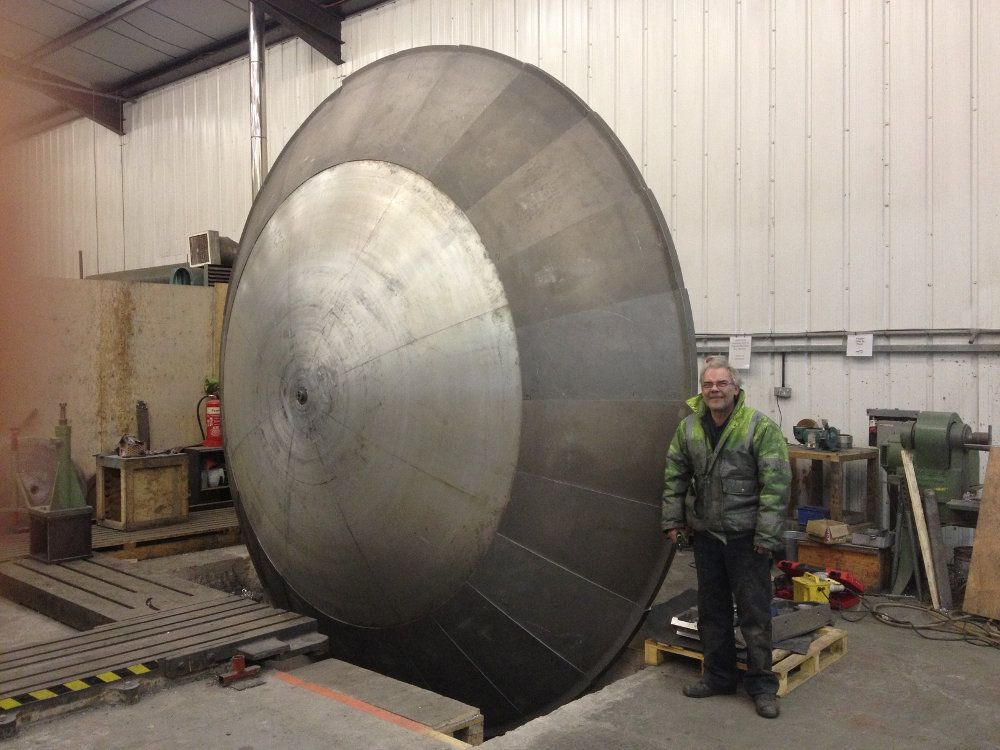
Fig. 5. Turning the tool. The 2-axis slide is not at 90 degrees to the machine axis as this would require too much slide movement, Instead a minimal Y axis moving only 300mm or so is used, and an angular offset applied. The software is used in mill configuration using the radius of the lathe tool tip as an offset.
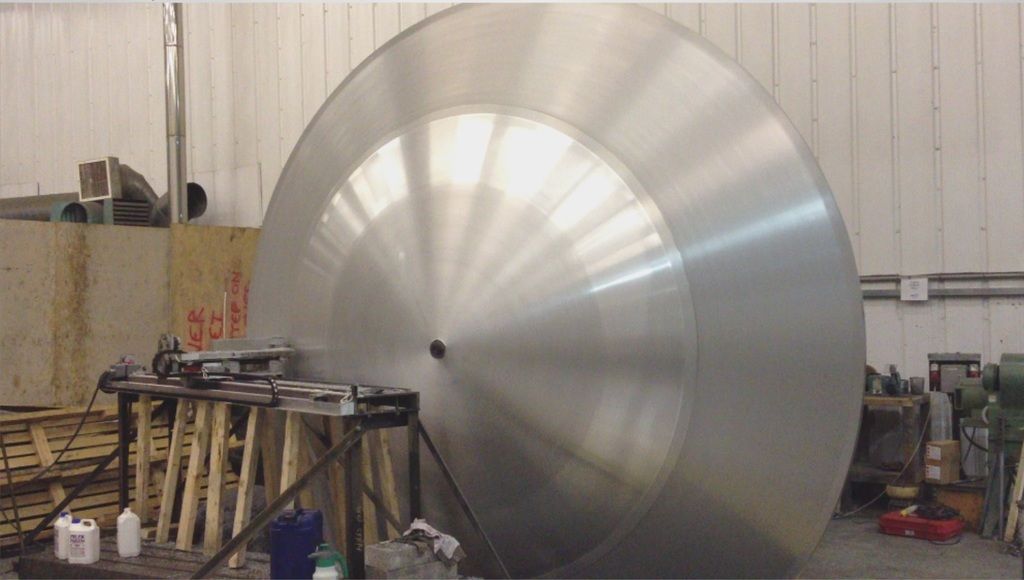
Fig. 6. The finished tool With its eventual operator for scale.
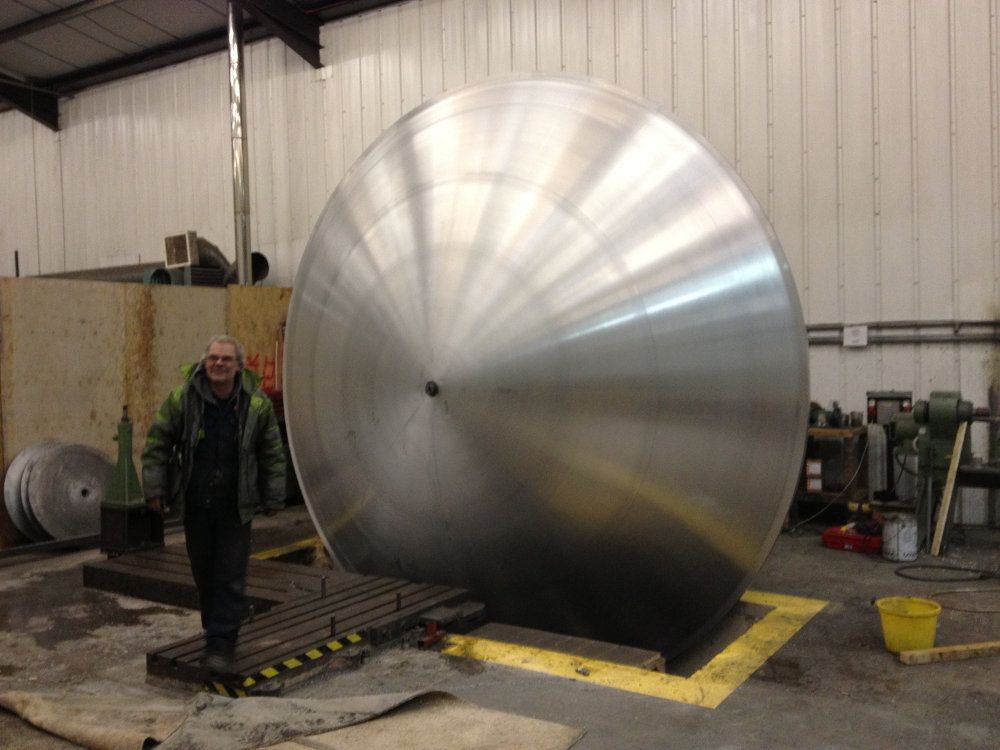
Programming was simple since a parabolic curve is simply defined mathematically, so parametrics are used to recalculate the next pair of X and Y coordinates based on a subroutine that runs several times a second to change the value of two parameters which are then translated to X and Y before movement. The program as it was run was about 30 lines long. This and the angular offset made the programming easy.
Turning took six days, day and night. This was a long job and the first I've seen where the job was bigger than the machine! a number of visitors called their friends and just said "get down here. You've got to see this". As far as we know this is the largest metallic spinning tool in europe - and it was made using Mach3.