I checked the kernel speed out sure enough it was set at 25000. how can it run at 2500rpm then?, it sure did!. I have now changed it over to 45Khz, so all's theoretically fair.
I changed the motor pulse time to see if that made a difference on the vibration, it pretty much didnt, all that happened was to increase or decrease the spindle speed, it didnt change the vibration.
I took off the drive belt from between spindle and motor and tried again, behold it was deathly quiet, apart from the inverter whistle!. I think I can concllude that the belt was tracking off and up the side of the timing pulley flange, the lumpy profile of the 5MM HTD belt was just 'biting' on entry to the pcd form on the pulley, if you get what i mean, a case of mis-alignment. Its caused from the OEM motor mount plate bieng fixed in only two places, which is quite lame, but then I guess it wasnt intended for a heavier motor and drive, and also was driven by a plain old V belt so there were no notches or teeth to mis-bite.
The OEM motor mount plate is 4mm thick, it's thick enough but it only has two points of contact inside the machine, one to pivot on and the other one slot/bolt to nip up once you have taken up the belt slack. I could physically move the motor if i pushed it hard and it wasnt sitting parrallel to the spindle, so the belt was just running off to the edge without the 3rd point of contact to guarantee parrallel.
So next stop is to machine up a larger plate, so I can fix in three place at least, where arrow is!. I wasnt oblivious to the flexing issue, i just wanted to check the software side, thanks very much for the advice :-) .
suprising they got away with it before!

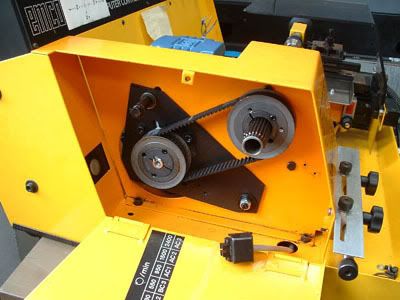