Hi all
Not sure if this is in the right section but here goes.
I purchased a 2nd hand tabletop 3axis engraver/milling machine about 12 months ago and have finally managed to get it working sort of anyway.
However it has no provision for home stop switches just X,Y,Z and spindle control. The controller/ driver is housed in a blue box with a spindle speed control knob on the front. (cheap chinese model)
I have purchased a TB6600 stepper driver off ebay as I wanted to have home stop switches and be able to control the spindle through software.
Unfortunatly I'm confused about the wiring for the spindle as to me it does not make sense. Looking at the wiring diagram the power goes straight from the power supply to the spindle and then on to the controller. To me that would mean that the spindle would be running at full speed all the time and not really controlled by the controller.
Here's the wiring diagram.
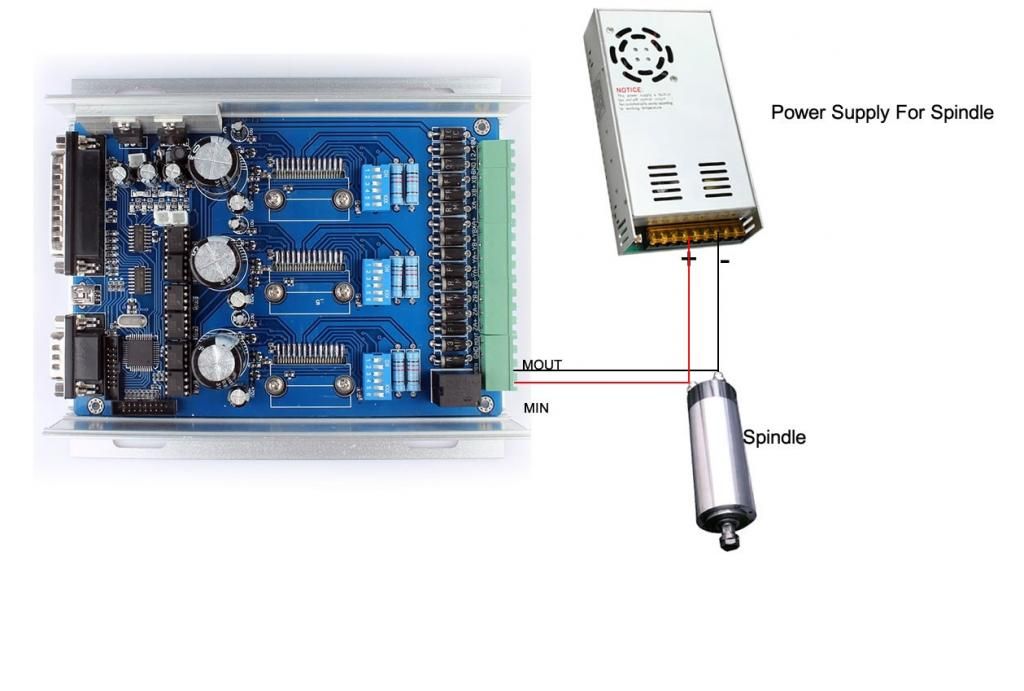
[/URL]][/img]
And this is the controller
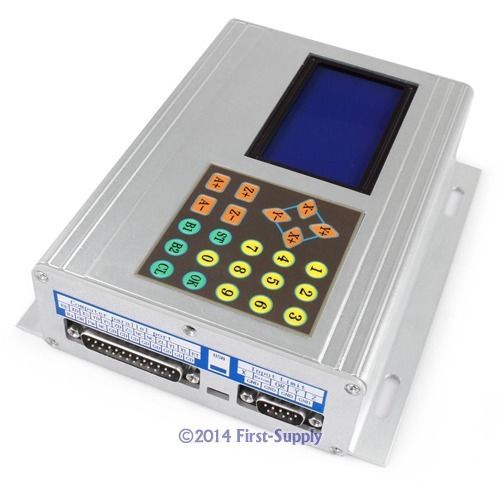
[/URL][/img]