Hi people!
I'm Johann from the Netherlands.
Bought an old BPi412 a while ago.
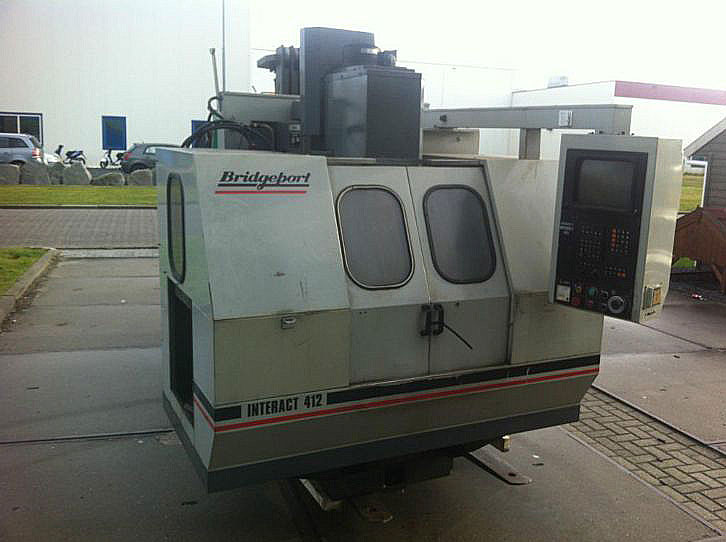
Machine was supposed to have lost it's parameters. Price was accordingly and some tools came with the machine.
After receiving the machine it turned out the parameters were still there but the Bosch servo amp had a problem.
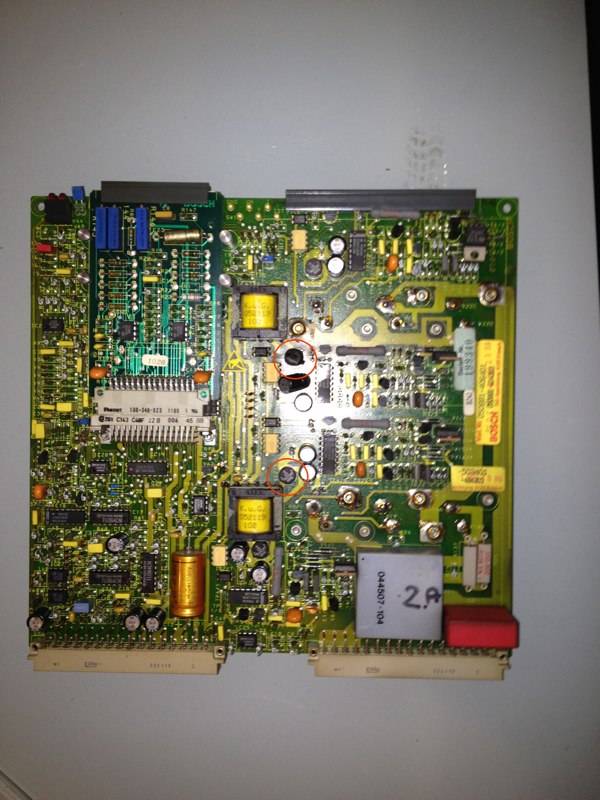
An attempt to repair the amp didn't work out so I decided to replace the servo's.
To at least be able to use a mill I ran in to another BP, a 308, at an auction and also bought this fully functional machine. While working with the machine with a HH 2500 control I came to the conclusion the 2500 was a tad to limited for what I wanted to do. A fun machine and with CAM software things were possible but communication and also the machine's memory are slow and limited.
It got me thinking about the BPi412 with it's HH 355 control. After checking on servo drives it also turned out that the encoders make things difficult or expensive better said.
Eventually I decided to rebuild to Mach3. A bit of a gamble. Not much experience with Mach nor G-code but I thought it was nice challenge.
This forum has been a great help to get to that decision. Next question was about the setup. Which controller to use and which servo's. Eventually I decided to use a CSMIO/IP-S in combination with 750Watt Delta ASDA-B2 servo's.
Not having electrical diagrams of the machine made it an even bigger challenge.
While waiting for the Bosch amp repair I partially took the machine apart.
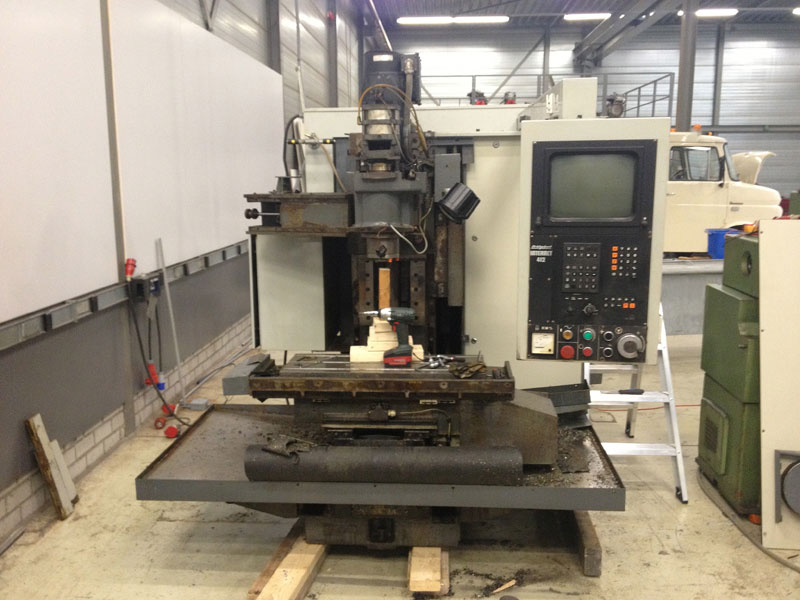
This to clean up the huge mess inside the machine and also to paint the inside of the machine white to make it appear a bit less depressing, a bit more light inside. I want to keep the outside as old looking as it is.
Also repaired the ATC,
Before,
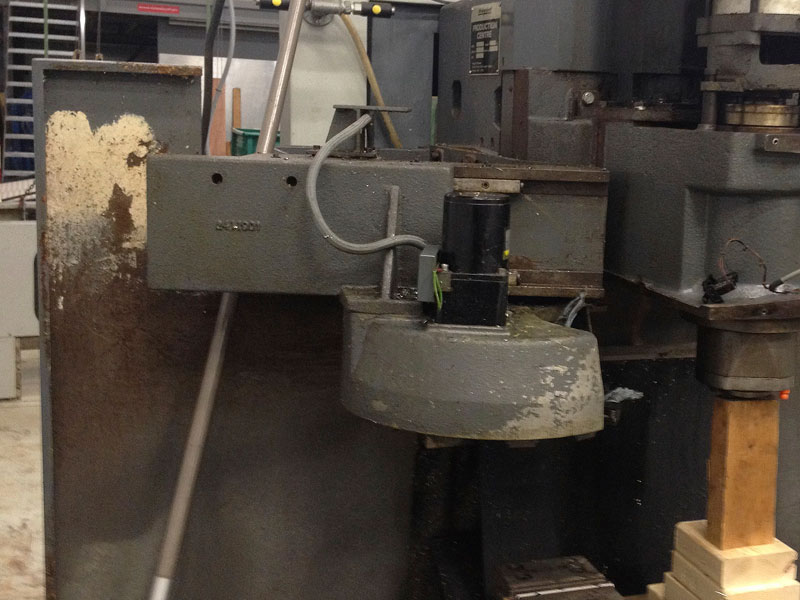
After,
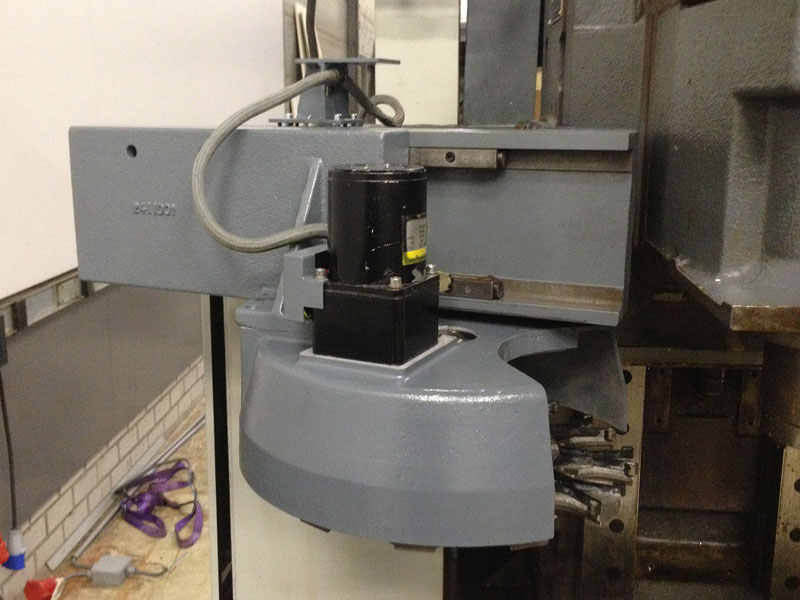
Welded a crack in the turret mount and replaced the bearings. Cleaned everything and added some paint and grease.
After receiving a Delta servo motor I made new mounting plates for the motors and ordered new pulleys and belts,
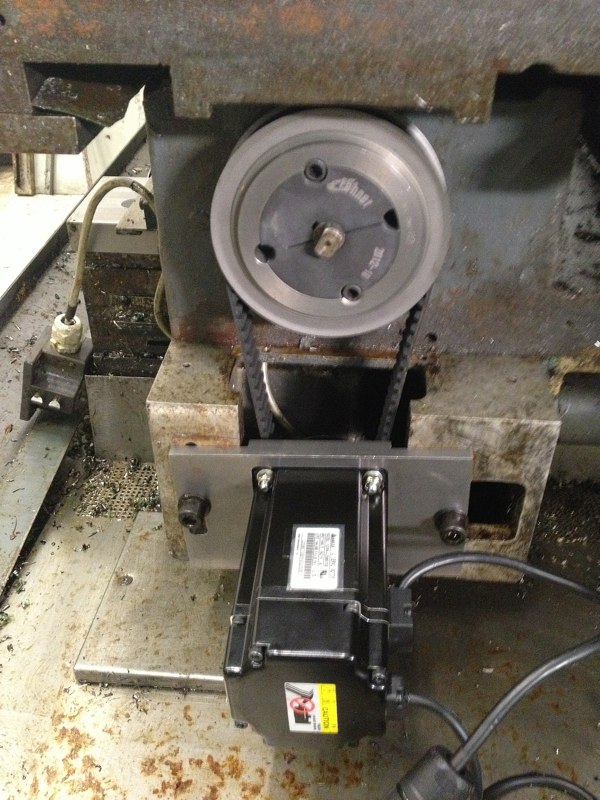
Removed the Bosch cabinet from the machine and made a new placeholder for the Delta drives,
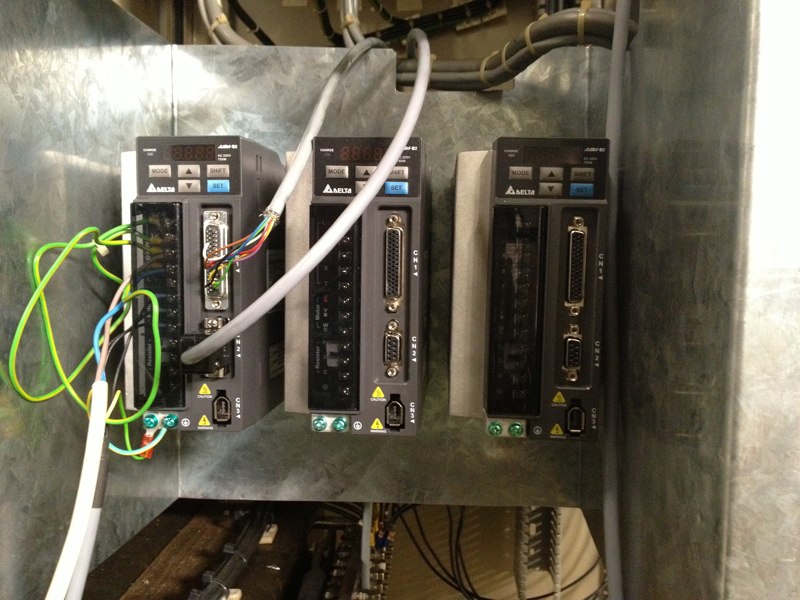
About three weeks ago I ordered a CSMIO straight from CS-Labs in Poland. Also ordered an MPG unit with it. Removed most of the electrical parts from the machine. Managed to find a very bad quality diagram of the machine and discovered that I had removed to much from the cabinet..

After 5 days the CSMIO arrived and I started rewiring the cabinet. The Fanuc Spindle was a bit of a headache but eventually I managed to trace all the pins. Got the Fanuc working with the CSMIO. Spindle Orientation is also functional. Reused the ATC motor and used the original wiring with it. Basically managed to get all the OEM parts working. Only tested one drive so far because I'm still waiting for cables. Drive appears to work well. Needs some fine tuning when everything is in place.
Not being an electrical guy I think the cabinet looks pretty neat so far,
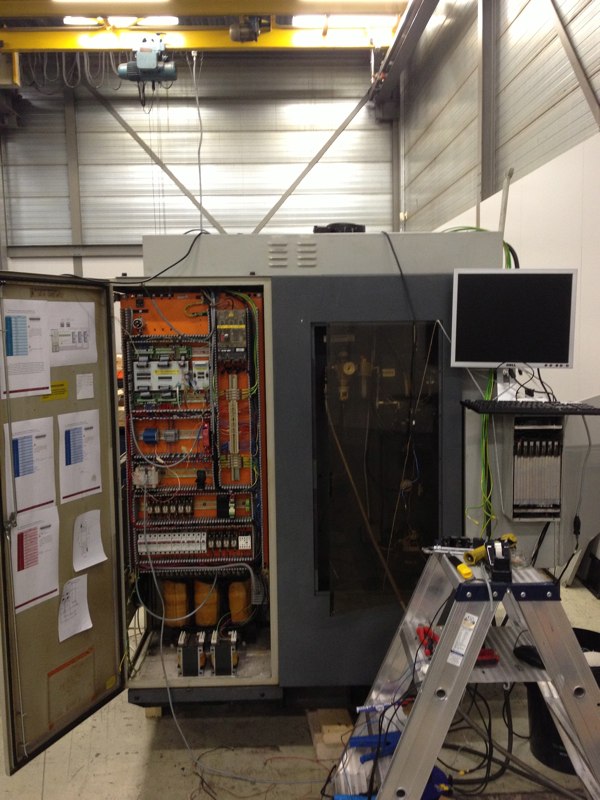
My biggest fear is the ATC. Did a lot of reading on this forum and decided to take a look at, the amazing, JHChoppers's
script.
After having the pneumatics up and running I did some trial and error testing. I'm not a VB scripter by any means but after about an hour I managed to get the ATC to initialise and count pockets. Somehow the LED's of the Airblast, tool release and ram movement aren't working but the buttons are doing what they're supposed to do. Orient needs to be done. No clue about monitoring the Fanuc spindle though.
Just wanted to share and also thank JHChoppers for the great script.