I don't come here much, but I was posting a Q in the VB section and was going to add a few more pics to my 'mini machining center thread'. I tripped over this thread

Unfortunately I do not have time to really read the entire thread at this time, but in skimming, I found a couple of items that I may be able to clarify.
1) Bearings side loading: I also spoke to SKF engineering long ago and got the OK and the specs to preload their deep groove precision plus bearings. This makes something of a 'po boy' angular contact bearing although you benefit only from the zero backlash and do not get additional precision. In fact, the lack of precision can cause slight 'tight spots' in the rotation which would not be present in preloaded ABEC7 bearings.
2) There was mention of bearing install specs. This is a valid discussion, but the large OD of the 5C spindle results in such a friggin huge bearing, only the alignment spec (which is pretty wide, especially for the typical C3) really needs to be considered. If you have a 4,000lb armature spinning on these size bearings (a more appropriate use) then heat transfer and so on become important considerations. I am now completing an all new prototype 4th axis which will have for the first time a precision option with ABEC7 AC bearings. To meet that spec, the assembled frame will be line bored. I am going to do them all that way, but it is not needed for the deep groove ball bearings.
3) Belt Type: Technically, the trapezoid form is tighter and is still 'good practice' spec for positioning as was mentioned in this thread. How . . ever, other than being an easy tooth form to make pulleys for, it has nothing else going for it. They are very noisy and have far less power capacity that HTD or GT. Part of the good positioning performance comes from the tension spec, which is sort of 'cheating' in my view. There is a 'secret' to tightening up the GT that I will share here for the first time; cut the teeth a little bit (the spec I will not share) shallow. This compresses the teeth into the groves and eliminates the tiny amount of backlash that is intentionally built into the form. You can probably duplicate this effect in an of-the-shelf pulley by machining a very small amount from the tops of the teeth. Since this is likely to reduce the overall belt life, I am not recommending it . . . . I'm just saying . . .

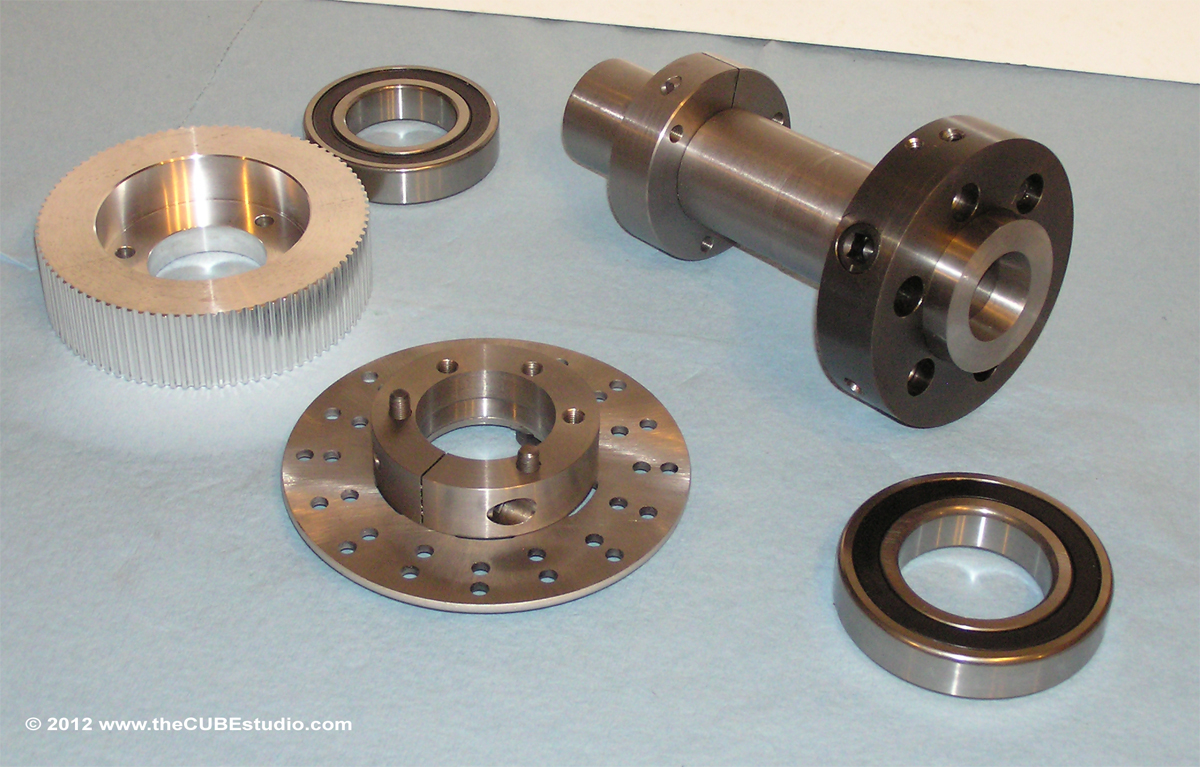