i stored this machine for 3 years, along with the PC, (hello again) and recently just pulled it out of storage. Funny thing is nothing worked properly, mach was crashing, spindle not keeping speed.
good news is thanks to forums and members posting i seem to have gotten through some of the initial problems.
First problem, spindle index pulse reading upto 1500rpm then counting half ! after that, so i changed the index debounce to 0. where as before it was 400/100 . i changed it to 150/0 in the debounce bounces and it reads well now at any speed. i also have spindle speed averaging checked, the 's true' fluctuates a few rpm like 4 or so i think its o.k, its a low inertia drive at high speed so its never going to be digit perfect
Second, actual spindle speed: i've spent many attempts trying to cal the spindle, but it always left a dip about 1600-1700 rpm.
i realised that dependant on the number you put into the spindle pulley max, that dip either got worse or better on screen
I cant say how important it is to know the actual rpm of the motor from the decal plate, its been a few years and i just thought it was 2940, well, of course all the readings were way off, duh, the motor max was actually 2790rpm. face palm time. so i tried all kinds of settings 2940 right down to 2000, with different velocities.
after finally putting in the correct resulting speed into pulley max (2511rpm@100% mach out)
i got a fairly linear calibration, with a small dip , heres a shot:
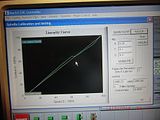
after the cal completed i tried commanding speeds throughout the rev range to see what happened, it was about 20rpm+ plus out on each 200 interval, so here's what i did, i went into the spindle motor tuning and dialled back the spindle velocity a little, about 25 units at a time, and then rechecked the commanded speeds. i took about 50 units of the total (it was 1500 before). and now its fairly close and linear through out the rev range within 5 rpms at bottom end, upto about 2000 its still within 5-10, get to 2500 its 50rpm out.
its been a week of late nights, it can make dog meat of you easy!
some settings are here if it helps anyone with a similar set up:
for reference, my index pulse disc is 4" diameter and the slot is 0.460" wide, mounted on the back of the spindle. i'm using a c3 pulse board and sensor.
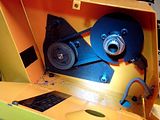
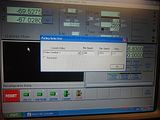
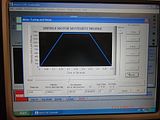
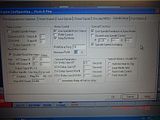
next problem i have is on the main power supply, i am too close to 50vdc on my stepper drives , and they trip / protect themselves regularly when other 1-2kw items switch on the same power supply line (heater)
I appreciate some help here, my PS is as follows;
240ac into ring core transformer which gives 35ac out, rectifies into dc thru bridge rectifier GBPC15005
I have a 63Vdc 22000uF capacitor before the drives. both drives are attatched to cap.
what is the best way to regulate the drives?