261
Show"N"Tell ( Your Machines) / Re: Denford ORAC lathe retrofit.
« on: August 04, 2013, 11:06:56 AM »
After further review, I added a manual cutting oil flow control knob to the oil dispenser. I’ve been making a few parts with the ORAC lately and found that different cuts wanted more or less oil. I could change the flow rate during the cut but had to walk around behind the machine & tweak the pump control arm. Not cool!
Never ignoring a chance to use stuff in my junk drawers to rig up a Rube Goldberg (Heath Robinson for my English brethren) contraption, here’s what I came up with. The bellcrank & connector widgets were from my R/C model airplane drawers. The rack & pinion remote cable was given to me back in the 80’s. Dunno what it was made for but it works smooth as silk and was perfect for the job. Anybody else got packrat disease as bad as me?
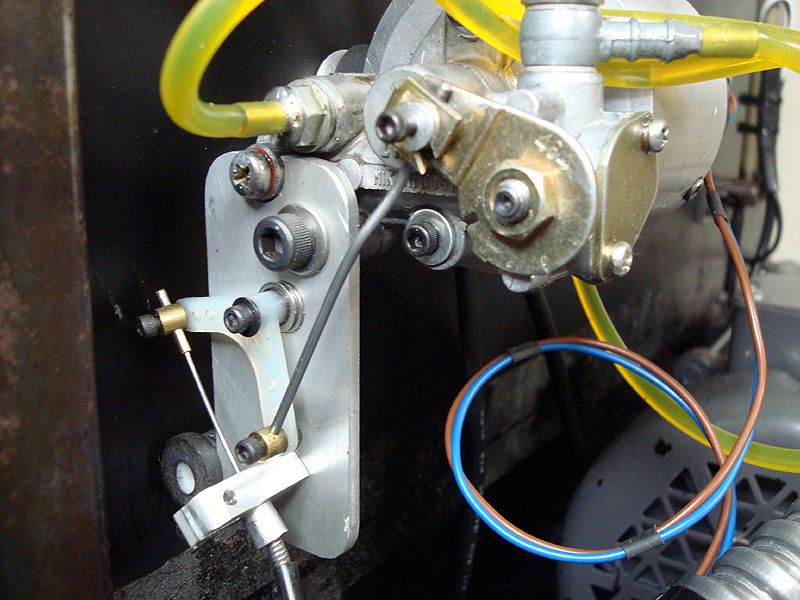
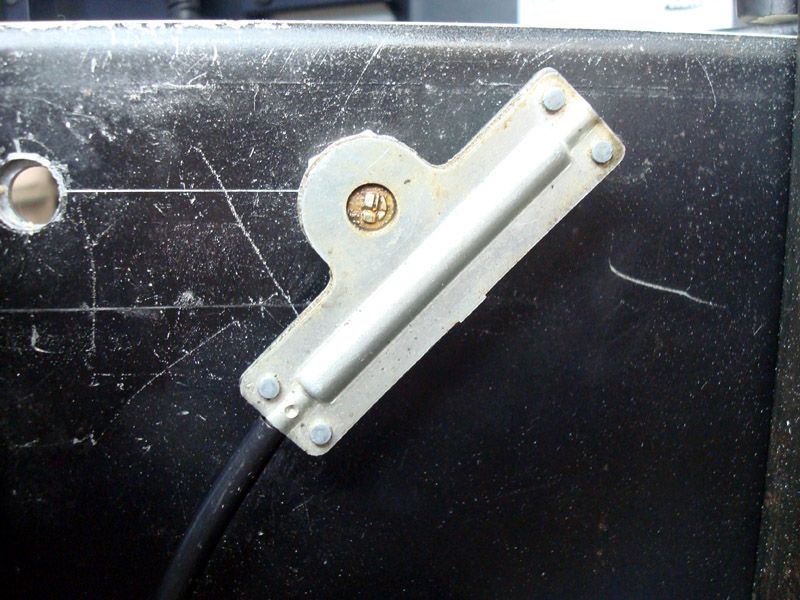
I’ve been messing around with my Denford MicroMill (runs on Mach3 & W2000) and made a little label plate to go under the knob. The little thing does a pretty decent job! Funny, even after a lifetime of adjusting carburetor needles & turning water faucets CCW to increase the flow, my automatic instinct to increase the oil flow was to turn the knob CW like a volume control. Brain defect I guess. That’s why the wacky linkage was used. Sidenote: Pi$$ed me off when I used acetone to clean the ORAC graphic before sticking the label on & found out Denford screen printed the clear film on the outside!
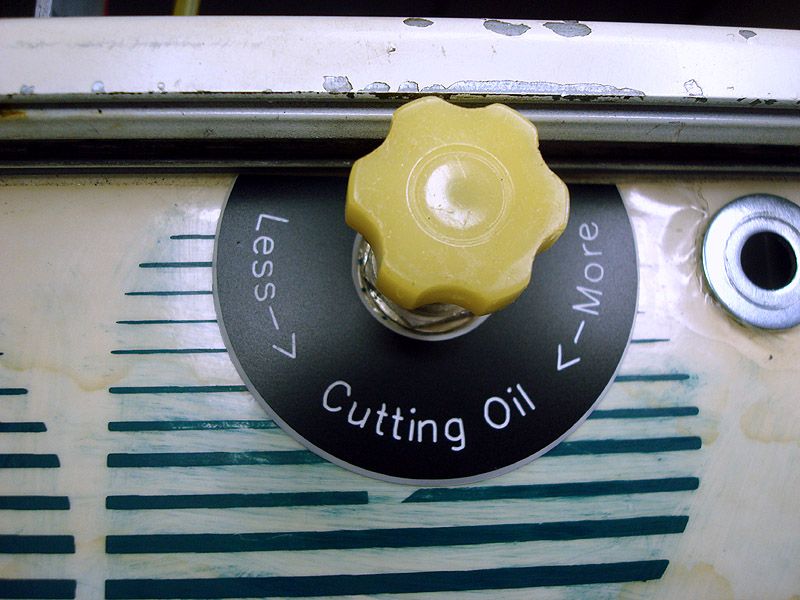
-
Never ignoring a chance to use stuff in my junk drawers to rig up a Rube Goldberg (Heath Robinson for my English brethren) contraption, here’s what I came up with. The bellcrank & connector widgets were from my R/C model airplane drawers. The rack & pinion remote cable was given to me back in the 80’s. Dunno what it was made for but it works smooth as silk and was perfect for the job. Anybody else got packrat disease as bad as me?
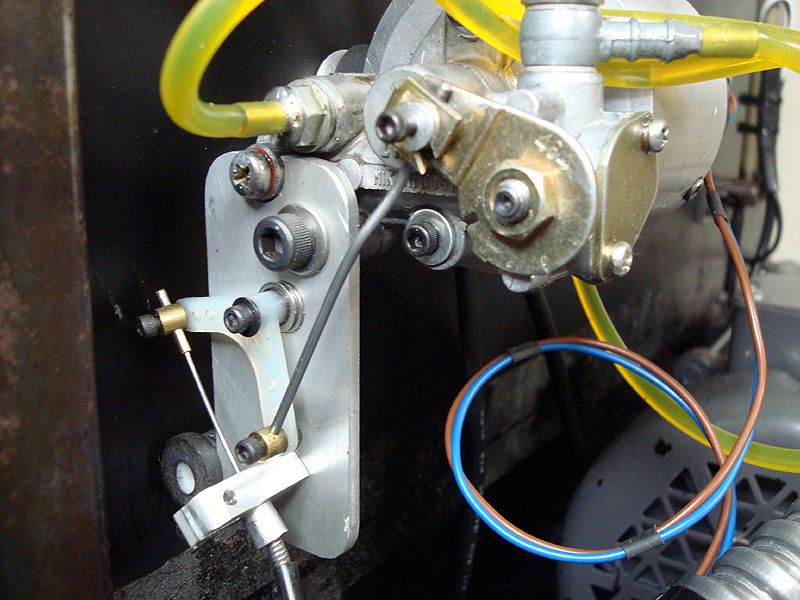
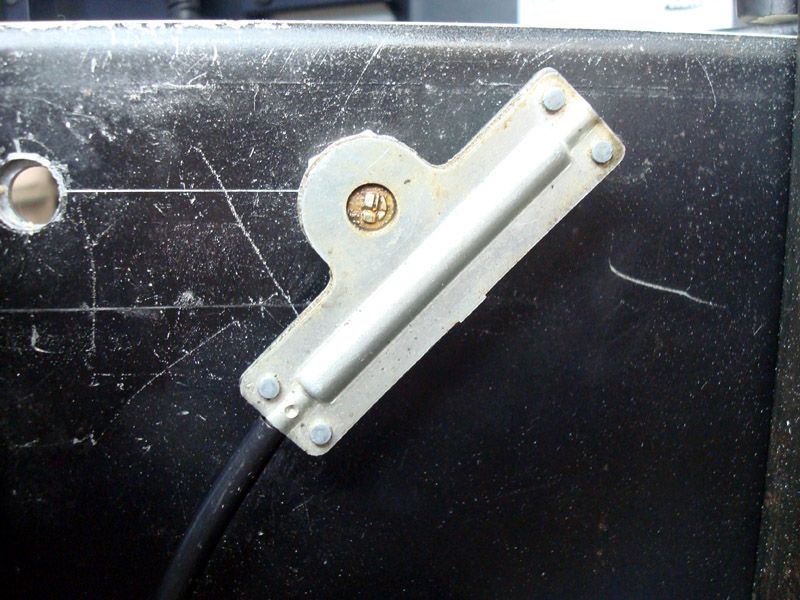
I’ve been messing around with my Denford MicroMill (runs on Mach3 & W2000) and made a little label plate to go under the knob. The little thing does a pretty decent job! Funny, even after a lifetime of adjusting carburetor needles & turning water faucets CCW to increase the flow, my automatic instinct to increase the oil flow was to turn the knob CW like a volume control. Brain defect I guess. That’s why the wacky linkage was used. Sidenote: Pi$$ed me off when I used acetone to clean the ORAC graphic before sticking the label on & found out Denford screen printed the clear film on the outside!
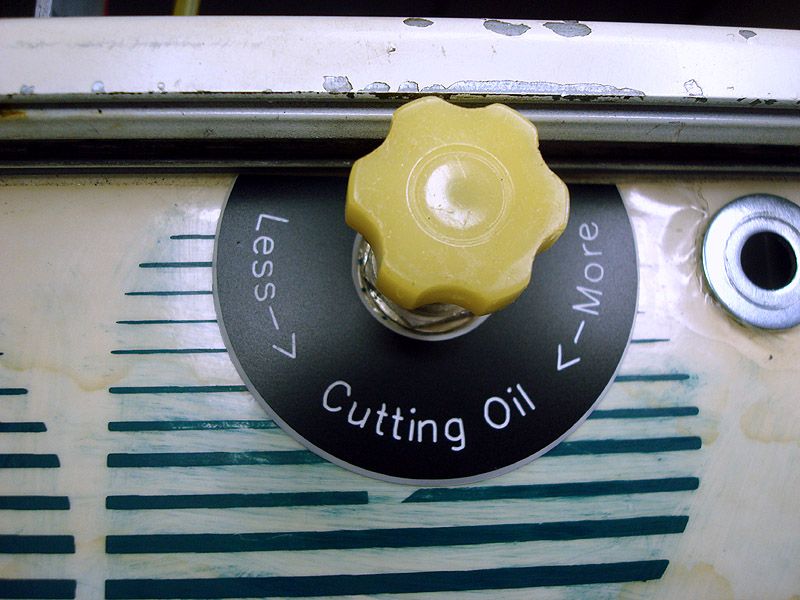
-